BMAC is conducting an analysis of Canada’s essential minerals processing capabilities with the goal of completing the battery value chain that is essential to the country of the United States net-zero future.
The Battery Metals Association of Canada ( BMAC ) published a plan for Canada’s battery value chain in 2022 with the goal of realizing the country net zero future. This roadmap presents a national strategy to enable Canada to take advantage of its plentiful mineral resources while even guiding its net-zero future in collaboration with the Energy Futures Lab, Accelerate ZEV, and The Transition Accelelerator. A thriving electric vehicle market necessitates an abundance of materials like nickel, lithium, rare earths, and cobalt, to name a few. Essential materials go hand in hand with the natural transition.
With the expansion of refining and production capabilities, Canada, which is abundant in both quantity and variety of essential materials, could quickly emerge as a leading worldwide supplier. The roadmap provides a thorough analysis of the French battery supply chain and its potential, including specific production timetables and targets as well as an in-depth action plan for the complexities, difficulties, and steps that must be taken.
A Strategic Roadmap for Building a Sustainable Battery Supply Chain
The action plan has four objectives, the first of which is to maximize the development and refinement of essential materials in Canada. This is an important component of Canada’s Critical Minerals strategy, which aims to increase supply and improve access by promoting the development of existing projects as well as the exploration of new projects, both of which can take up to 15 years.
Goal two proposes the creation of a world-class processing industry and relates to the chemical stage of the battery supply chain. The second focus examines the middle of the battery production chain in a similar manner, assessing Canada’s manufacturing potential and ability for further collaboration and line-up improvements. Recognizing the constantly rising demand for batteries and novel battery technologies, Canada could excel in this field thanks to its wide range of modern capabilities.
Recycling and finishing the battery supply chain are the third and final objectives of the roadmap. The circularity of resources is necessary for a battery chain that is really responsible. The value of creating a closed-loop battery recycling industry that will allow Canada to sustain the supply chain and the demand it intends to meet is discussed in BMAC’s roadmap.
BMAC aims to comprehend the realities of effective and economical implementation in relation to all four objectives, including the necessary funding, technological advancements, and possible legislation. For a thorough analysis demonstrates Canada’s possible to build an effective, integrated battery supply chain that will foster innovation and draw in foreign investment while aiming to achieve an international net-zero economy.
Canada’s vital mineral processing capabilities.
The roadmap presented its findings, identified and prioritized the following steps, and came to a conclusion. The need to create mid-stream essential minerals processing capabilities that would close Canada’s existing supply chain gap was one of the important findings. For instance, battery-grade lithium is created through the processing of the mineral extracted from spodumene and brines.
Asia now controls the majority of the world’s lithium processing capabilities, necessitating the export of excavated lithium for refining and processing before importation for the production of batteries. The supply chain is being made more difficult by Canada’s lack of local processing capacity. The development of a world-class chemical industry, which involves completing the supply chain from extraction to production, is the logical second step given the abundance of mineral resources. As a result, Canada will be able to support French battery companies, maximize its resources, and expand its export market.
BMAC evaluation on key materials
BMAC is currently conducting an analysis of Canada’s vital minerals processing capabilities in response to this discovery. The goal is to determine the best ways to properly implement material processing capacities in a way that is both internationally competitive and, ideally, net-zero.
The evaluation will focus on eight key materials: Lithium, nickel, copper, graphite, iron, phosphate, vanadium, and rare earth elements (REEs).
The eight essential components for batteries
There is some uncertainty regarding the potential market dominance of battery chemistries. The nickel-rich higher energy batteries that are already in use require significant amounts of nickel and cobalt, both of which are costly to obtain. In the electric vehicle industry, switching to lithium-iron-phosphate batteries is less expensive but does not offer the exact energy density. There is also a need for innovation, and Canada can best get ready by looking into various materials that will probably be used in novel applications.
BMAC has enlisted specialized industry experts for each of the materials it has selected to offer advice on the best processing techniques and technologies for the various types and grades of materials available in Canada. BMAC has received expert feedback through a number of interactive virtual workshops before applying their knowledge by reviewing the resulting flowsheets.
To determine where and how processing these crucial materials would be most effective and lasting, they will be assessed against important questions.
Canada’s opportunities to process the important materials
Where there is lively mining or exploring mining potential in Canada is a crucial factor to take into account. The best locations for processing crucial minerals may now be those that are already in use, reducing the distance that local materials must travel for refining and processing.
The criteria for choosing the regions with the best processing capabilities are still up in the air. Furthermore, it’s possible that there are many factors that will differ between metals rather than a single set of criteria. Each group of metals experts will, however, offer a set of suggestions. This is just the start; BMAC will also conduct follow-up work to investigate and define possible opportunities, particularly in relation to the creation of battery hubs in Western Canada.
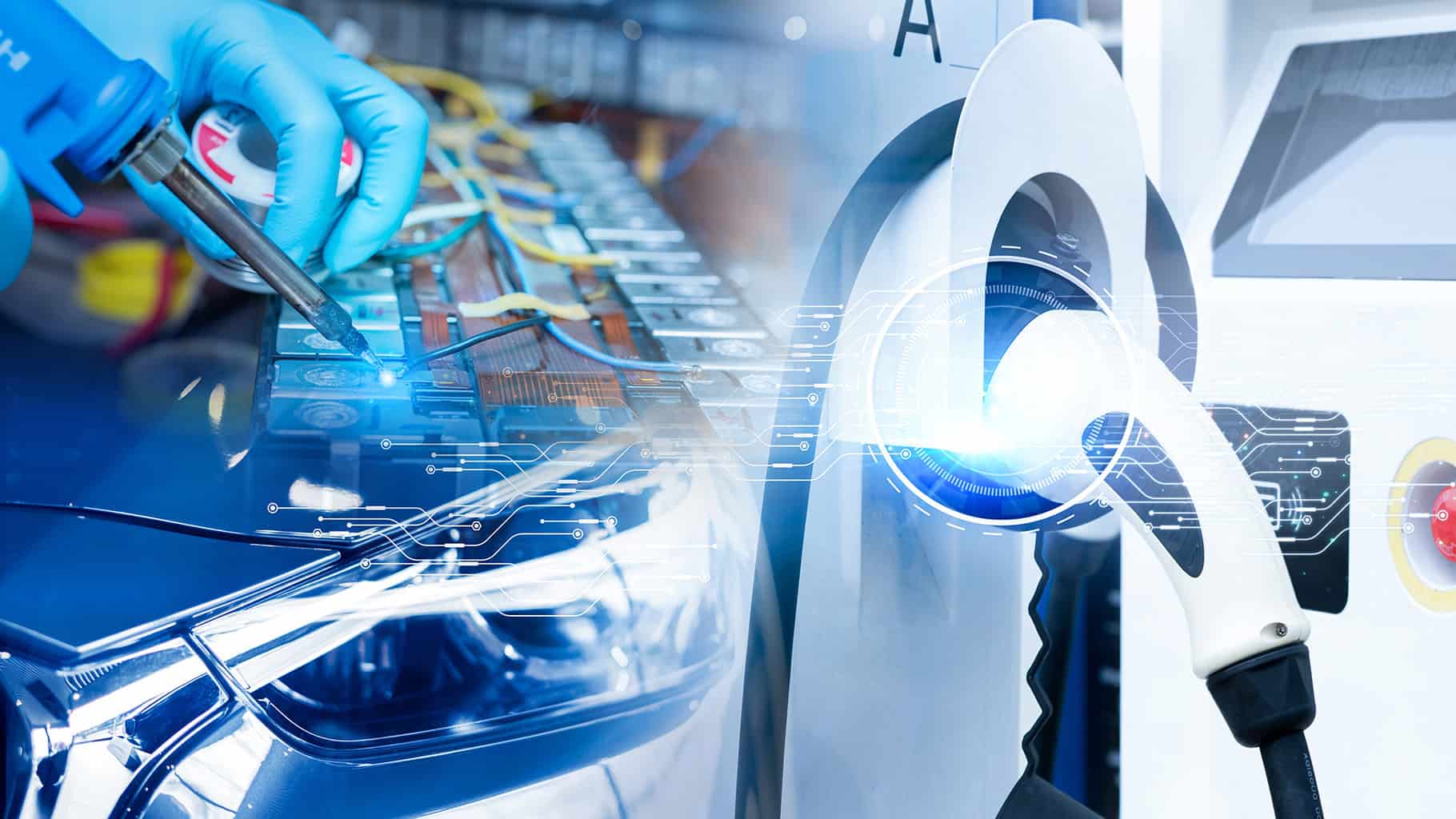
BMAC’s Roadmap for a Low-Carbon Battery Metals Supply Chain
The goal of the roadmap is to create a supply chain for battery metals that is both aggressive and long-lasting. Existing battery supply chains are carbon-intensive and harmful to the environment, despite being essential to our net-zero future. BMAC acknowledges that a decrease in carbon footprint will be necessary for battery supply chains to survive, and that strengthening Canada’s position in the world battery market should be done to ensure its longevity. In order to accomplish this, the analysis aims to identify supply chain improvement areas and find ways to reduce the carbon intensity of processing each of the important materials. These areas include technology, travel, and energy efficiency. The creation of essential minerals processing facilities in Canada would establish a local supply chain and significantly lessen the carbon footprint of processed metals that are exported.
Separately, BMAC wants to start a new project that involves the American value chain’s ESG modeling and calculations. Due to the complexity of these calculations, the analysis will start by taking the carbon element into account. This research could gradually look into the various possible effects of building processing facilities, such as their effects on regional communities, the economy, and upcoming legislation.
Optimizing Material Flow: Canada’s Lithium Resources for Sustainable Supply Chain Solutions
Every production and coordination process, which refers to the effective movement of materials throughout the entire supply chain, must take into account the best flow of the materials. Ideal flow, in essence, has the lowest impact while still being the most dynamic design, preventing delays, cutting costs, and improving efficiency. In order to achieve the online zero goal and demonstrate the most cost-effective and effective solutions, this will work to find those with the least climate impact.
The lithium deposits in Canada are the best example of how each material has distinct characteristics that call for it to be addressed singly and fully.
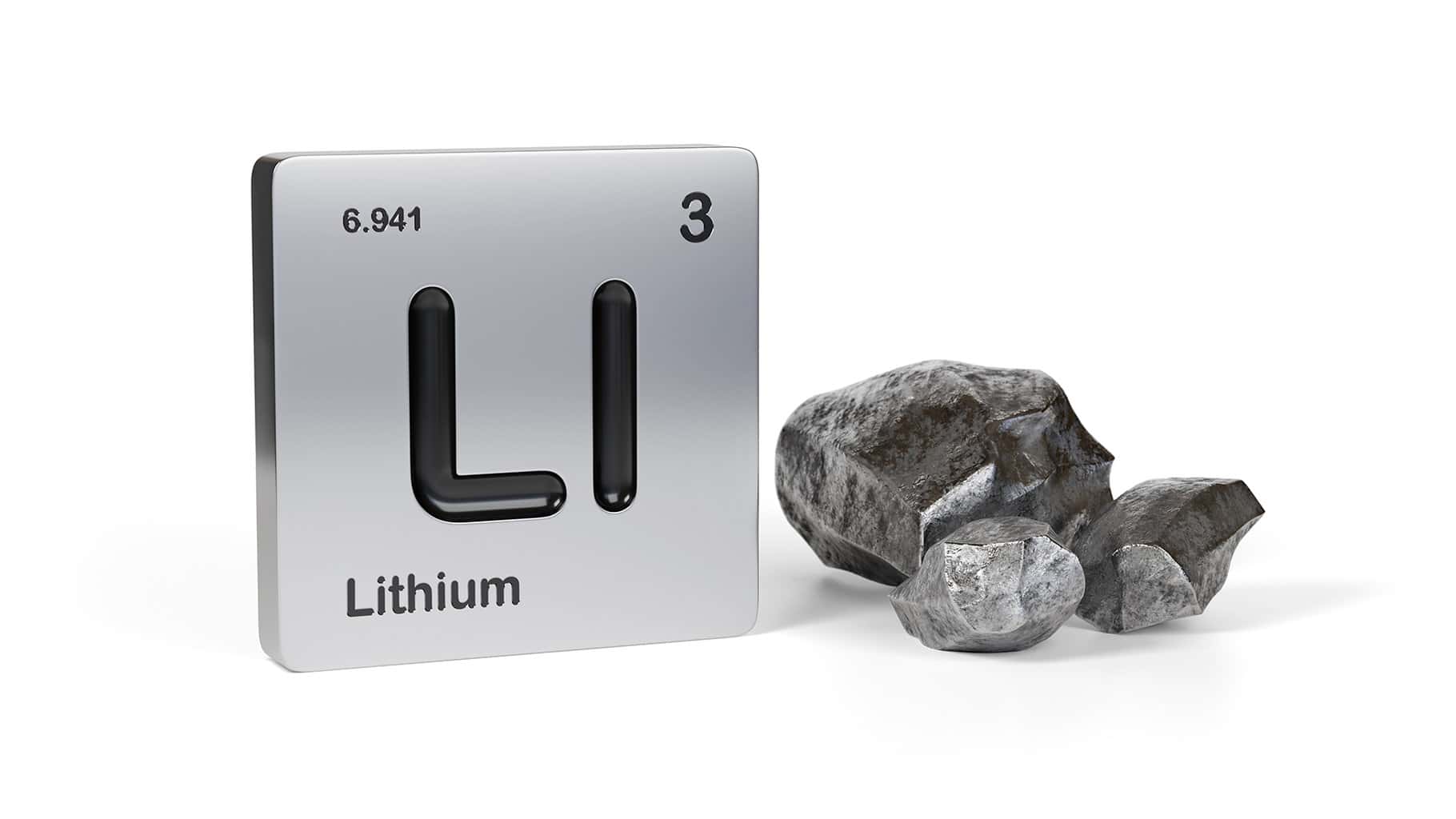
Both spodumene and brine, two types of lithium, are abundant in Canada. Hard rock spodumene deposits, which are mined before going through leaching and purification to produce battery-grade lithium, are mostly found in the south. In the West, lithium dissolved in water is found in brine-based lithium resources. The brine-based lithium industry is being transformed by direct lithium extraction ( DLE), and a number of startups are positioned to mass-produce lithium by 2025–2027.
As a result, BMAC’s work aims to address the evolution of these two wholly different processes in its analysis of lithium. Since the supply from both will probably be required to meet rising demand, flowsheets for both hard rock and brine-based lithium will be produced. As a result, the report will determine whether one source is better suited than the other for particular processes rather than endorsing one over another.
Strategies for Developing Sustainable Battery Value Chains
The goal of the roadmap was to meet the government’s requirement for 100 % ZEV light-duty vehicles by 2035 while also reiterating the 10 % market share of North American automobiles currently held by Canada. For these objectives to be achieved as well as for enabling a lasting value chain, it is essential to develop Canada’s  , essential minerals processing capabilities.
In Canada, it can be challenging to set a specific deadline for completing the native value chain. This is due to a number of unidentified factors, most notably the fact that we are unsure of the battery chemistries that Canada will produce and, consequently, the demand for the necessary materials. Given the likelihood of cross-border collaboration in the production of EVs across North America, it could be argued that the value chain does not have to be fully completed for all essential materials.
The BMAC’s metals strategies will pinpoint essential areas and best processes that can be used to close the gap and move materials from extraction to production in order to develop Canadas mid-stream processing capacities.
The evaluation hopes to provide comprehensive flowsheets that can direct Canada’s battery value chain. BMAC anticipates these strategies will be released around mid-2024, with the follow-up work of the value chain opportunities for Western Canada completed by the end of the year.