Go2Lithium is transforming the lithium extraction industry with its advanced continuous Direct Lithium Extraction (cDLE®) technology. Their cutting-edge counter-current processing system significantly improves lithium capture from low-concentration brines, achieving higher efficiency and lower costs than traditional methods. This unique approach allows for scalable operations, flexibility in handling varying feed concentrations, and reduced pretreatment expenses. At the core of their innovation is the pilot plant at LithiumBank’s facility in Calgary, which demonstrates the viability of their technology. By focusing on ion exchange sorbents, Go2Lithium enhances lithium concentration from 100 mg/L to over 3,000 mg/L, making the process more cost-effective and environmentally friendly. The integration of graphene membranes and the Clean-iX® process further underscores their commitment to sustainable lithium extraction. These technologies offer pre-treatment with nanofiltration and economical removal of impurities, helping lower the operating and capital expenses (capex and opex) of lithium refining. Go2Lithium’s advancements have profound implications for the future of green mining practices, positioning the company at the forefront of responsible and efficient lithium production for energy storage and electric vehicles.
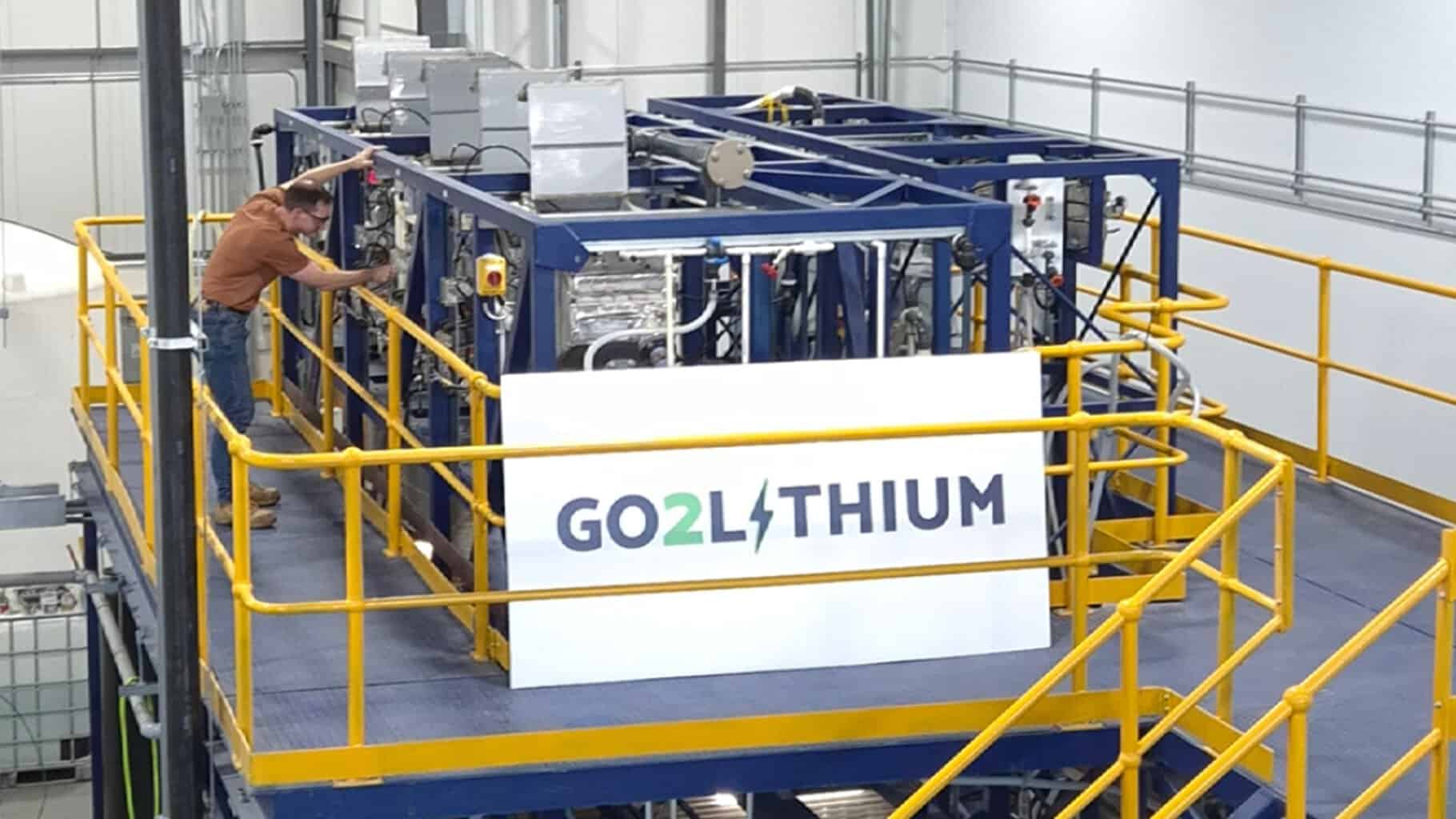
A novel technology has been developed by Go2Lithium to make it easier and more affordable to extract lithium from low-concentration brines.
With its cutting-edge technologies and forward-thinking initiatives, Go2Lithium is changing the lithium extraction industry. This article delves into Go2Lithium’s unique continuous counter-current processing technology, the advanced continuous Direct Lithium Extraction ( cDLE® ) method, and the recent milestone of opening a pilot plant at LithiumBank Resources Corp. ( LithiumBank ) facility in Calgary, Canada.
cDLE® steady counter-current processing technology
Go2Lithium’s ongoing counter-current processing technology is a major leap forward in lithium extraction. cDLE® is a genuine moving bed process, where the sorbent is transferred between the unit processes of sorption, washing and desorption. Depending on the lithium concentration, the total dissolved solids, and the particular impurities in the brine, the cDLE® process can use either an ion exchanger or an adsorbent.
In low-concentration brines, such as those with less than 100 mg/L Li, ion exchange is the recommended method in the cDLE® process. Thanks to its higher loading capacity and, eventually, lower desorption volume requirements, ion exchange offers faster and more intensive lithium capture and upgrade than adsorption. With the proper ion exchangers, 100 mg/L Li in the feed brine can be upgraded to over 3, 000 mg/L in the DLE product, demonstrating the efficiency and cost-effectiveness of the cDLE® process.
When comparing DLE processes based on fixed beds, such as simulated moving beds ( SMB carrousels, ISEP, Septor, Puritech ) or lead-lag desorption, to cDLE®, significant differences become apparent. The cDLE® process, by its nature, can handle a more changing feed flow, feed lithium and impurity concentrations, including suspended solids, and can use lower-cost chemical reagents. This unique adaptability of the cDLE® , process can substantially reduce pretreatment expenses, making it a more cost-effective and practical option.
The sorbent for DLE is a subject of debate. Adsorbents, especially those based around aluminium, have a long history of use and are generally considered to be a lower risk. Nevertheless, the decision to use adsorption must also consider the trade-offs. Adsorption may result in a lower risk, but it also results in a lower lithium upgrade and more freshwater use, necessitating a larger refining procedure with related capital and operating costs. This discussion highlights the complexity of the choices that the lithium extraction industry must make.
The ion exchange sorbents are a relatively new innovation and, thus, have not yet been used extensively in commercial plants. Like the aluminium-based adsorbents, the ion exchangers are usually minerals based on either chromium or titanium oxide mineral components. Due to the higher lithium loading capacity, ion exchangers offer a much better build potential, which is beautiful. Because the ion exchanger is content to a lot of pH variations during processing, it needs to be both physically and chemically robust. The use of chemistry is portrayed as a disadvantage for ion-exchanging processes. However, it must be said that adsorbents also need chemicals and broad water management, albeit in the refining stages of the process.
It is crucial to understand the entire economics and make the choice regarding the sorbent and the process, taking into account both the pretreatment and refining aspects, because the mechanical flow and purity of the DLE eluate have a significant impact on the capital and operating costs of the lithium refining stages.
The purpose of cDLE® technology is to carefully target and increase the concentration of lithium ions while ensuring that impurities are primarily rejected. The moving bed approach allows the use of lower-cost chemistries for pH control, with lime being used in sorption and sulfuric acid in desorption. The ion exchange sorption and desorption processes are both carried out using the counter-current process.
The moving bed process is incredibly flexible and modular. The constant nature allows for easy expansion as demand increases, making it a flexible solution for both small-scale and large-scale operations. In practice, moving bed processes have been operated at a corporate scale for the recovery of nickel, cobalt, scandium, vanadium, and uranium.
cDLE® pilot plant at LithiumBank
The new opening of LithiumBank’s cDLE® pilot plant is a major milestone for Go2Lithium. One of the largest DLE pilot plants in North America, the facility has a processing capacity of about 10,000 L/d of brine. The pilot plant will demonstrate the company’s cutting-edge technologies in practice in a real-world setting.
The pilot plant will be used as a platform for Go2Lithium’s technologies ‘ testing, allowing the business to refine its procedures and demonstrate their viability on a commercial scale. Located at LithiumBank’s Calgary facility, the cDLE® pilot plant is carefully positioned to take advantage of local lithium brine resources, ensuring a steady supply of raw materials for continuous testing and optimisation.
The pilot plant is a hub for collaboration with industry partners, researchers, and stakeholders, fostering an environment of innovation and knowledge sharing to drive more advancements in lithium extraction technology.
Implications for the lithium industry
Go2Lithium’s advancements have far-reaching implications for the lithium industry. By enhancing lithium extraction’s efficiency and sustainability, Go2Lithium is opening the door for a more socially conscious supply chain.
The increasing need for green mining practices aligns with the use of cost-effective chemical reagents, lowered water usage, and minimal environmental impact.
Lower operating costs are reduced as a result of increased extraction efficiency, making lithium more accessible and affordable for a range of applications, including energy vehicles and alternative energy storage.
Future of lithium extraction
As Go2Lithium continues to innovate and refine its technologies, the future of DLE lithium extraction technology looks appealing. The use of constant counter-current processing technology in cDLE® offers a blueprint for successful, sustainable, and flexible lithium production, and the pilot plant at LithiumBank serves as a testament to these advancements.
In addition to reducing the capex and opex of both the DLE process and with pretreatment and refining, Go2Lithium continues to innovate in the DLE lithium extraction space. The use of graphene membranes during pretreatment and the use of Clean-iX® constant ion exchange for impurity removal are two examples.
Graphene membranes, operating as genuine molecular sieves down to 1, 000 Daltons, offer pre-treatment at the nanofiltration level without rejecting salts. High flux is obtained at low energy use because salts can successfully pass through the membrane.
The Clean-iX® process provides very economical and cost-effective removal of calcium, magnesium, boron, sodium, and potassium and can be easily coupled with concentration steps of reverse osmosis, forward osmosis, evaporation, and electrodialysis to complete the refining processes to battery-grade lithium salts.