The adoption of 3D digital twins in facility management is transforming how buildings are monitored and maintained, thanks to real-time data integration from IoT systems. These geographic digital twins provide virtual replicas of buildings, allowing facility managers to simulate renovations, track inefficiencies, and optimize building performance. Combining BIM (Building Information Modeling) with digital twins enhances planning, providing detailed insights throughout a building’s lifecycle. Predictive maintenance becomes more reliable when paired with digital twins, reducing false positives and maintenance costs by offering accurate, context-rich data. In sectors like construction and real estate, these innovations have significantly improved decision-making and long-term planning. While digital twins streamline operations, their success depends on proper implementation. Facility managers must ensure their smart building systems are compatible with the new technology and identify key use cases, like maintenance or renovation simulations. As smart building technology continues to advance, integrating digital twins will become a critical factor in maximizing IoT investments and improving facility management practices. By understanding their benefits and overcoming organizational challenges, property developers can unlock new opportunities and streamline operations with these cutting-edge technologies.
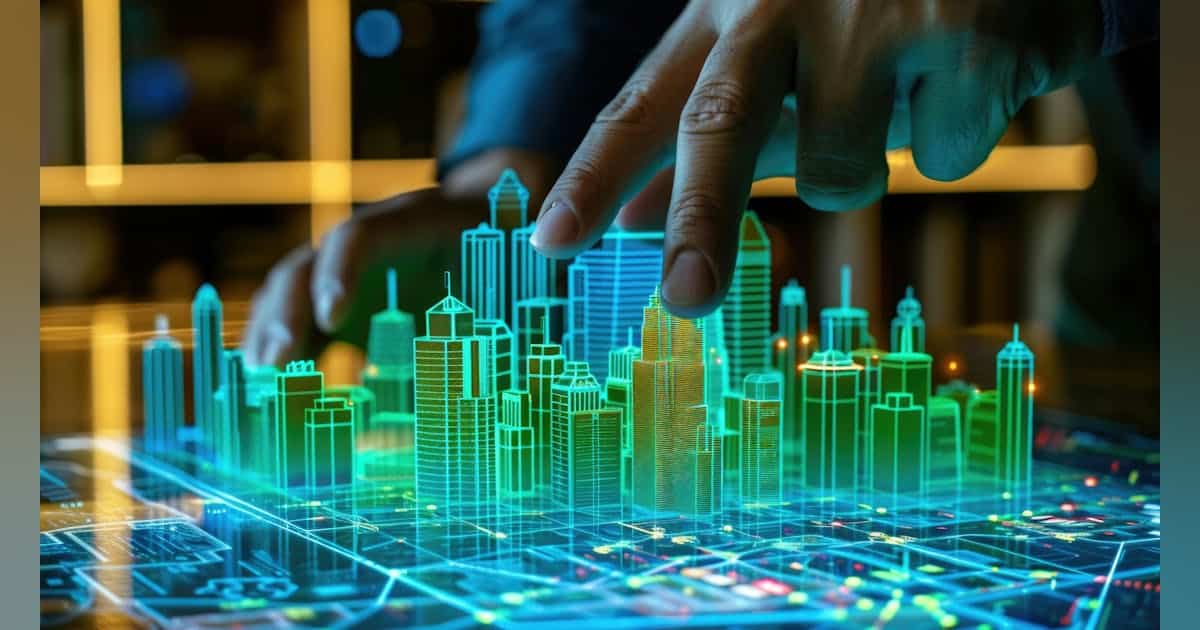
In the field of building and construction, modern technologies have made important strides. This once-tech-adverse sector has mostly reversed course and embraced new tools, frequently to great results. Geographical digital twins are one of the most promising of these in the field of facility management.
Digital disruption has now been caused by BIM, which uses building information modeling, in all stages of planning and design. This foundation is expanded by 3D online twins. As the technology grows and develops, it could redefine the future of facility management.
What Are Spatial Digital Twins?
A modern twin is a virtual replica of a real-world system—in this context, a building or complex of buildings. These representations include current data from Internet of Things ( IoT ) devices throughout the real estate, in contrast to a straightforward digital model. As a result, the twin updates whenever something changes in the facility.
Although these models can be used to represent larger systems like value chains or logistics networks, the building sector is primarily interested in geographic online twins. A geographical or 3D twin distinguishes itself from a 3D twin who uses geographic data to represent a real object in 3D space.
This data may include geographic surveys, site scans, classic blueprints, and more. The more information, the better, even though there is no set minimum or cap on what information must be or where it comes from. The twin’s more accurate resemblance to the actual world is increased by producing a richer dataset, increasing its value.
Applications of 3D Digital Twins in Facility Management
Geographic online twins can be used by facility managers in a variety of ways. It can start actually before construction, as some digital twin solutions can integrate 360-degree imagery into BIM models, tying the virtual and actual from the beginning. This ensures that any updates made throughout the project will appear in the twin, providing detailed documentation along the way, while also providing context for architects and designers.
Making wise decisions about upkeep is made easier by having all this information in one place. The twin will reveal which building features have the greatest inefficiencies or which fundamental weaknesses might have an impact on specific upgrades. Also facility managers can use them to simulate potential renovations and calculate the impact on utility efficiency.
Additionally, 3D online twins make a great maintenance tool. Because they connect to real-time data, they can alert managers to emerging situations indicating the need for repair, enabling faster, cheap fixes. Any IoT system can perform this kind of predicted maintenance, but a modern twin makes it more trustworthy by integrating data with the overall structure.
That setting is vital because some predicted maintenance algorithms have high false positive rates. Some businesses have experienced increased quiet and no shield savings as a result of these errors. Because it incorporates information from across the entire facility, a geographical digital twin is less likely to result in these outcomes, thereby assisting in the identification of the causes of abnormalities.
Benefits of Digital Twins for Facility Management
3D modern twins have significant advantages for facility management operations across all use cases. Refined decision-making is the most urgent. When all the data you need is in one place, it takes less time to determine the best path forward for repairs, upgrades, or other changes.
Any IoT system can provide information that helps make informed decisions, but accurate application and interpretation of the information are required. As a result, the industry faces a substantial gap—while 78% of facility managers have embraced smart building solutions, only 36% have seen measurable improvements. Yet when organizations lack data science talent, digital twins can bridge the gap by providing a space to test actions and estimate results based on this data.
Additionally, online twin simulations are faster and less expensive than natural trial and error. As a result, they make significant facility upgrades easier to achieve, leading to better returns on investment.  ,
The practice’s benefits are also maximized by using 3D online twins to refine predicted maintenance. Property managers can prevent breakdowns and lower repair costs while avoiding fake positives by adding context. Therefore, continued expenses fall, and the functional complexities of predictive maintenance become manageable. These benefits, on a larger scale, enable buildings to maximize their IoT investments.
Best Practices for Putting Spatial Digital Twins into Practice
Of course, it’s essential to put things into perspective. Similar to intelligent building technology, geographic digital twins demand careful execution to produce successful outcomes. Considering three of the five biggest barriers to digital twins are organizational—namely, lack of knowledge, small technology acceptance, and not understanding their value—changing that begins with proper education and planning.
Property developers who want to use this technology should first be aware of where it can be used. Digital twins just worth the investment if organizations now employ smart building solutions because they require a lot of data and produce better results when combined with IoT systems.
Before purchasing a modern twin platform, facility managers should also come up with a distinct use case. Forecast maintenance is a significant function for several buildings, but some might benefit from imagining future improvements and renovations. Finding the best solution will be made easier by determining which is most in line with the particular property’s objectives.
When businesses are aware of how their 3D geographical twin will be used, they can compare providers to determine the best option. These decisions should factor in compatibility with existing clever building systems, IT budgets, data requirements, and ease of use. Additionally, it is crucial to take into account the history of a software vendor in terms of data privacy and any cybersecurity features.
New Opportunities for Facility Managers Are Unlocked by Digital Twins
The potential of geographical online twins for facility management is difficult to ignore. Capitalizing on these solutions will become even more crucial as the industry extremely relies on clever building technology.
Learning where and how to use 3D online twins is a must before applying them. You can use these solutions to take your intelligent buildings to the next level once you understand their potential and have some best practices in place.