The Institute for Materials Technology and Plastics Processing (IWK) at OST – Eastern Switzerland University of Applied Sciences leads the charge towards a sustainable plastics industry. Through research spanning eight fields, including innovative recycling routes and closed-loop systems with partners like FREITAG®, IWK pioneers solutions for recycling challenges. Initiatives in odor reduction, bioplastics, and chemical recycling underscore their commitment to circularity, shaping the future of plastics sustainability.
To achieve a round plastics industry, no’ one- size- fits- all’ solution will do, but a combination of different approaches will be required.
In 2022, 400.3 Mt of plastics were produced worldwide ( Source: Plastics Europe ). Understandably, consumers and legislative bodies are clamoring for more watchful resource use and change to create a plastics industry that is as climate-neutral as possible. The Institute for Materials Technology and Plastics Processing ( IWK, a division of OST- Eastern Switzerland University of Applied Sciences ), is attempting to assist in this endeavor.
The competence spectrum of the IWK is divided into the following eight research fields: Injection Moulding/PUR, Compounding/Extrusion, Composite Technology/Lightweight Construction, Joining Technology, Metal Manufacturing Technologies, 3D- printing/Additive Manufacturing, Simulation Design, and Material Analysis Component Testing.
The goal of all the competence areas is to combine science and practice to create novel, close-to-production, industrial-oriented solutions, and, as a result, to address the recent issues facing the plastics industry using the most effective materials, material combinations, and production technologies.
Recycling is one of the most crucial tactics for achieving the goal of a round and sustainable plastics economy, along with reuse and reduction. Under Professor Daniel Schwendemann’s direction, the Compounding and Extrusion team at the IWK uses a systematic approach to find the most efficient way to achieve circularity for each client-specific application. In the future paragraphs, some remarkable projects are presented. Based on the following creative, each of them explores a distinct recycling route.
Electrical recycling: Is it possible to close the loop or even recycle?
In the plastics industry, structural recycling is a well-established procedure that collects, cleans, sorted, and converts products that have reached the end of life into fresh raw materials once more. For most applications, electrical recycling is sometimes associated with down-cycling or there are no recycling streams at all, which would be the ideal scenario.
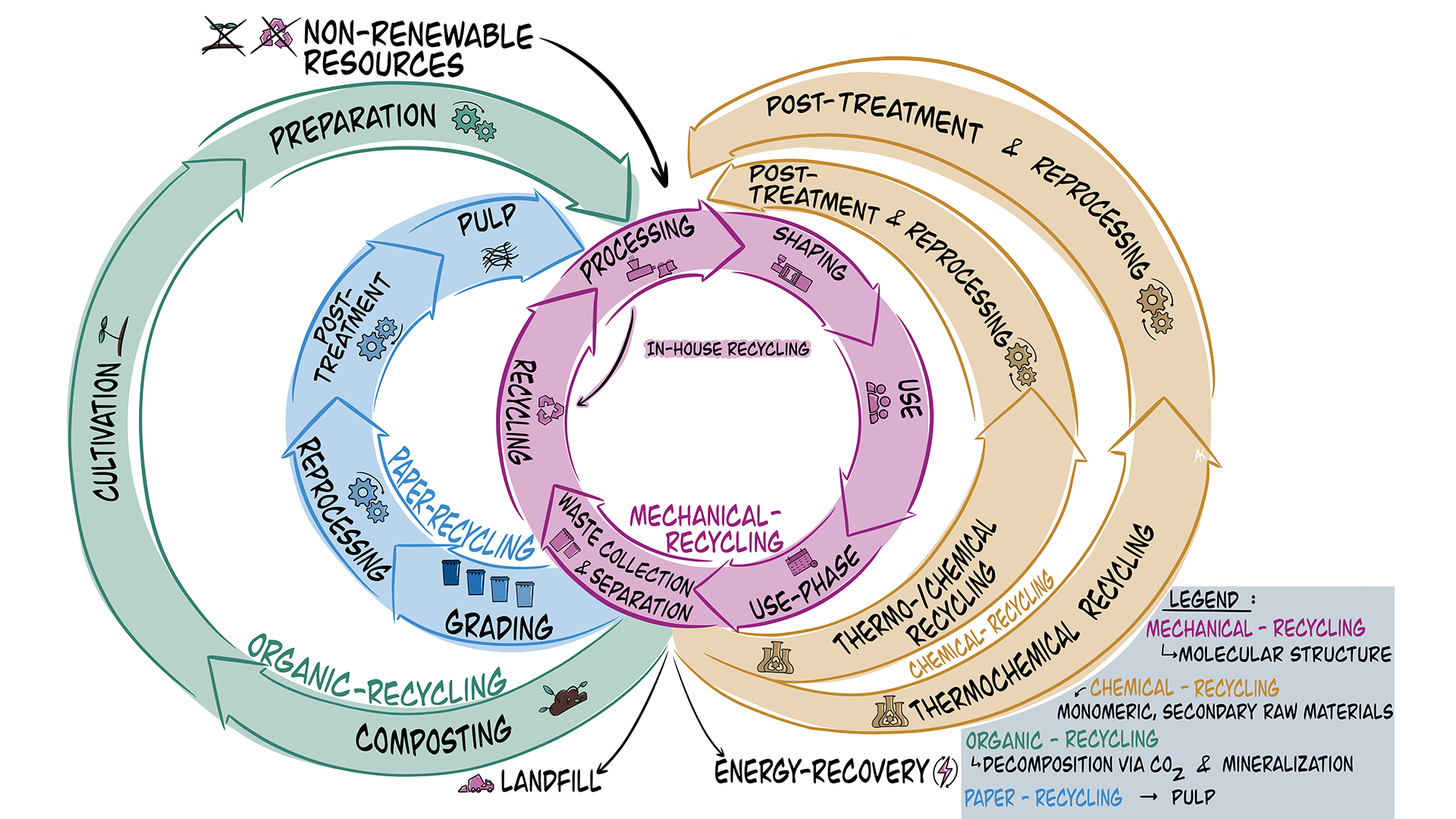
One of the projects addressing this problem is the F385 CIRC- System IPHONE®, a phone cover made of used ski boots, which was created in collaboration with IWK and FREITAG®. It demonstrates that a shut loop circle for used TPU ski boots is possible.
At ARGO in Davos, a workshop for people with disabilities, the ski boots are primary collected and sorted. The boots are dismantled, and all metal parts are separated. After that, FTIR can identify the polymer type, and the parts are color-sorted and shredded in a mill. The IWK compounder at the time the obtained flakes are processed to remove potential residual contamination and produce heterogeneous pellets.
The iPhone covers, which are subsequently produced via injection moulding, are made of 100 % recovered TPU and can be recycled again at their end- of- life within Freitag’s established Take- Up system.
The project highlights the potential of local production because the entire value creation occurs within 150 kilometers of Zurich, Switzerland, to create a finished material loop.
Odour reduction is one of the biggest challenges in electrical recycling, particularly for polyolefin materials like PE and PP. Probable process optimisations and material modifications were looked at in a project with Tide Ocean SA and the IWK. The objective was to have Tide Ocean SA’s ocean-bound rPE and rPP material meet the stringent standards of the mechanical industry standard VDA270.
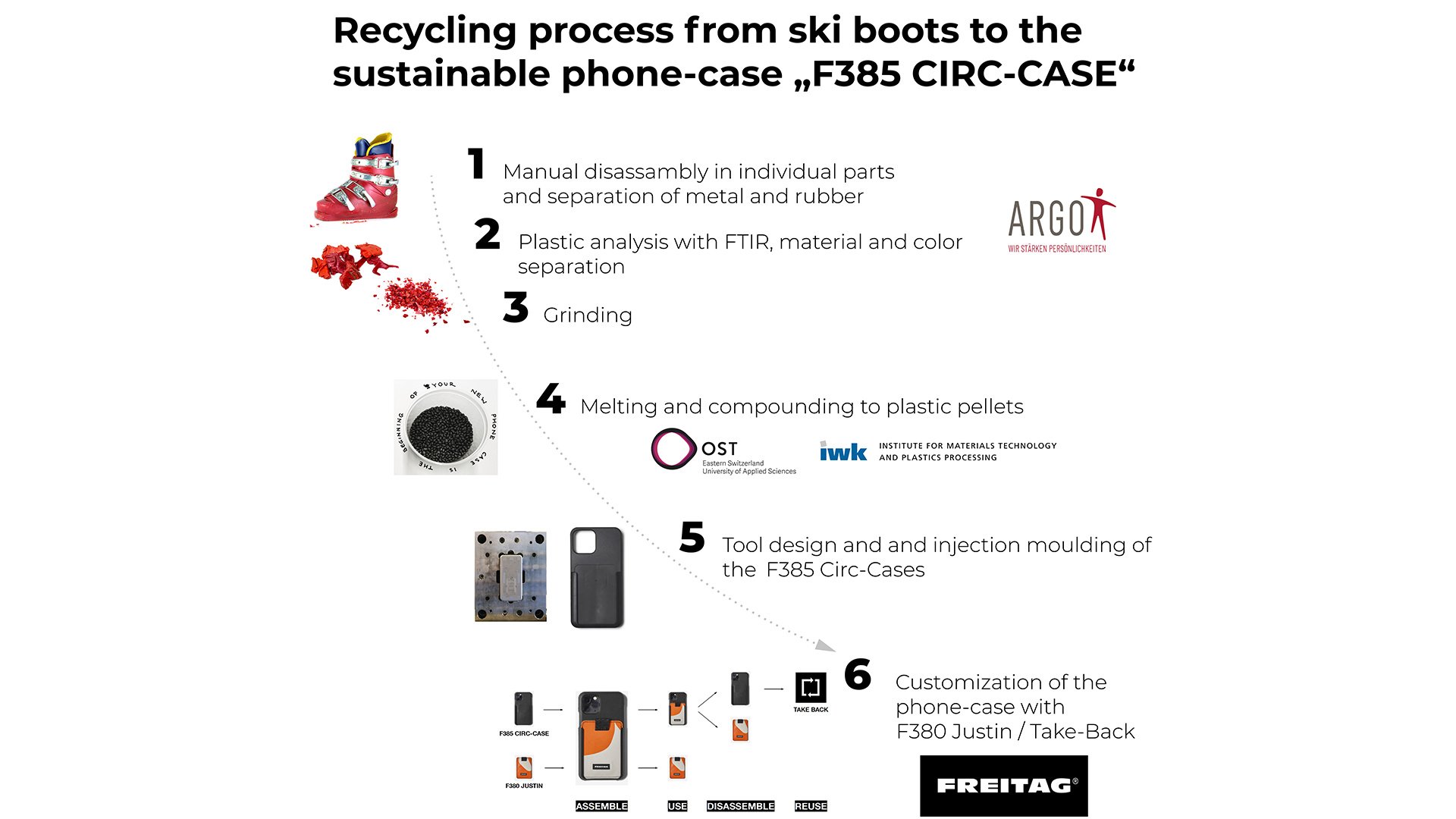
As part of a defined set of experiments, different screw configurations, degassing options, activation concepts, and the application of an entertainer for the removal of volatile organic compounds (VOC, source of odour development ) were tested. As a result, concepts for material and process optimization were created to meet the VDA270 requirements.
In addition to this project, Tide Ocean SA and IWK developed an impressive waste process and quality standards for collecting, sorting, compounding, and injection moulding that allows the production of higher- quality products from ocean- bound rPET. The granules can replace lady plastics without loss of quality in a variety of production processes, including 3D printing, textile fabrication, and injection moulding.
An example of powerful co- operation is a watch from Maurice Lacroix, in which the bezel, housing, crown, end, and closure parts are made from recycled ocean- bound rPET material.
Organic recycling – What is the impact of bioplastics?
The plastics industry is currently at the forefront of the use of bioplastics to replace regular fossil-based materials. But, bioplastics are even associated with several controversies, including competition with food and vague disposal/recycling routes. This is addressed by The FluidSolids AG, which offers materials made of extra materials that are 100 % compostable at home. Along with the IWK, the compound process was optimised, and scale- up was achieved. Biodegradable cutlery made of FluidSolids material can be found in European supermarkets today.
Paper recycling – Paper as a replacement for plastics?
Regulations and consumers are urging a reduction in plastic usage and the transition to other materials, especially in the field of packaging. In that context, the polymer industry is starting to realize that paper and paper-based materials have a growing amount of possible and importance. However, since the material and processing properties of paper are totally different from plastics, it is no trifling to replace them.
Founded by the’ Neue Regionalpolitik ‘ ( NRP ) of the canton Fribourg, the IWK, together with the iRAP ( Haute école d’ingénierie et d’architecture Fribourg ) and 11 companies investigated the feasibility of the potential of paper in plastic processes. Existing paper- based materials were examined, and their processability was tested successfully ( injection moulding, extrusion, thermoforming ).
The following steps, which are already being worked on in follow-up projects, were identified and translated into the identified and required adaptations regarding tools, content composition, and process parameters. The project demonstrated that paper-based materials are a useful addition to the existing material and property portfolio, even though they wo n’t definitely replace plastics in all ( packaging ) applications.
Chemical recycling – the future?
One of the biggest hopes for a round plastics industry is chemical recycling because it enables the recycling of mixed plastic waste and the recovery of virgin materials, something that is now impossible with mechanical recycling.
There are a variety of chemical recycling techniques, but none are currently used in business. This makes it nearly impossible to compare chemical recycling to electrical recycling in terms of their economic impact. But, it must be expected that chemical recycling will most likely have a higher energy demand and should, therefore, only be installed as a complementary recycling route to electrical recycling, for example, in textile recycling, where mechanical recycling is difficult due to the usually- high cotton content.
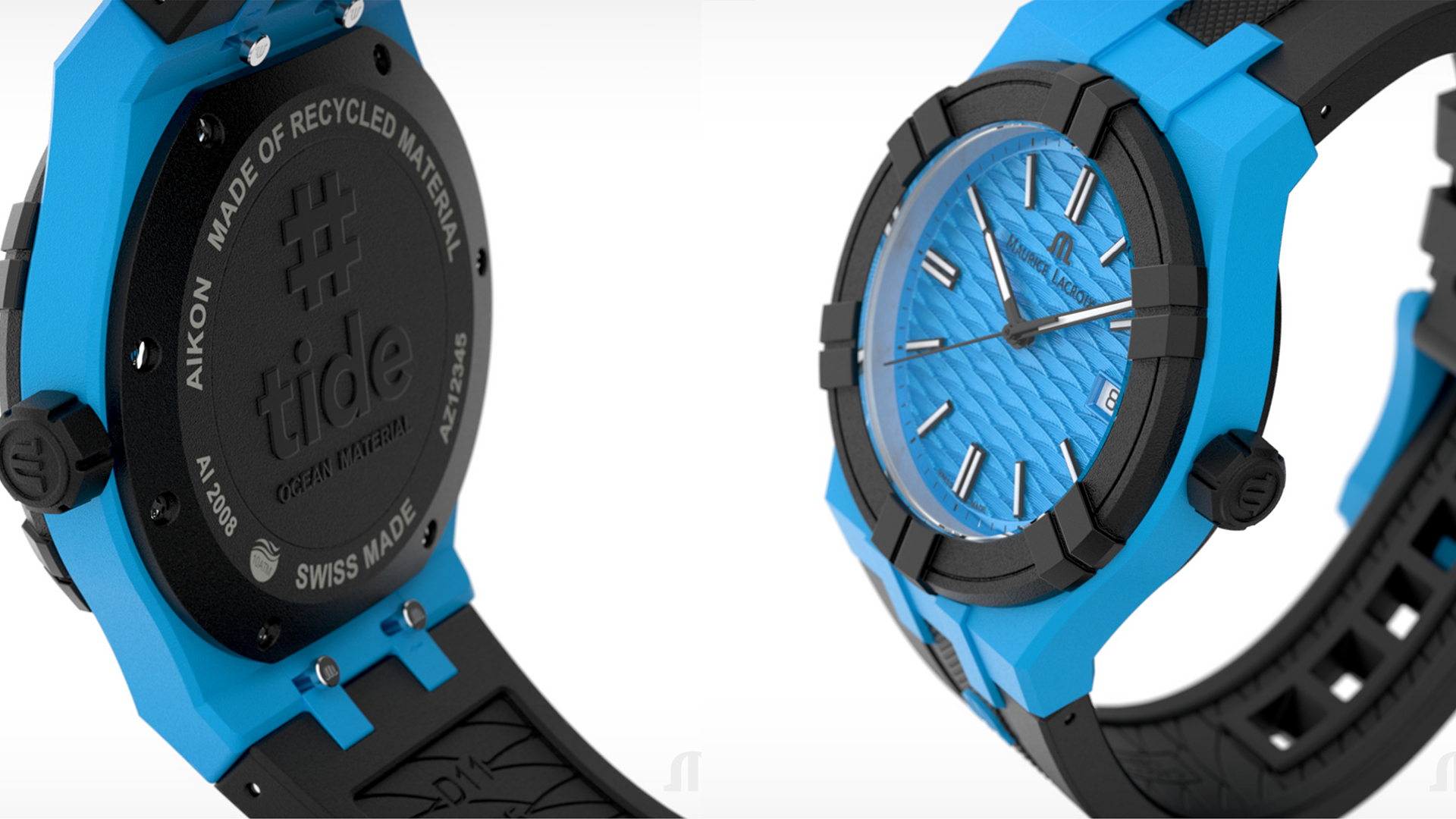
Summarising: Towards a Sustainable Plastics Industry
The plastics industry has many probable pathways toward circularity. Without taking into account the boundary conditions of the personal application, not” circle” should be favored over another one. In addition, the benefits of recycling technologies, both existing and emerging, can be beneficial drivers of sustainability.