A team from the University of Cambridge has pioneered a technique for Zero-Emission Concrete Production on a large scale, potentially revolutionizing net-zero emission efforts. This new approach leverages electric arc furnaces (EAFs), traditionally used for steel recycling, to recycle cement, the most carbon-intensive component of concrete. By replacing salt flux, usually used to remove impurities in steel recycling, with cement, the process produces a recycled material suitable for new green material production.
Concrete’s carbon footprint is largely due to cement production, which involves clinkering, releasing significant CO2 when heating limestone and other materials to around 1,450°C. Concrete is the second most-used material globally, accounting for nearly 7.5% of human-caused CO2 emissions. Reducing concrete emissions while maintaining supply is crucial for decarbonization. Although fly ash can replace up to half of the cement in concrete, it cannot meet the annual demand of four billion tonnes.
The novel recycling method incurs no additional costs for producing steel or concrete and significantly reduces the need for lime flux, thereby cutting emissions from both industries. Trials by the Materials Processing Institute demonstrated that recovered cement could be effectively produced in an EAF, marking the first large-scale production of this kind. This method could achieve zero-emission cement if powered by renewable energy.
Looking ahead, the Cambridge Electric Cement project aims to produce one billion tonnes of cement annually by 2050, about a quarter of current cement production. Supported by Innovate UK and the Engineering and Physical Sciences Research Council (EPSRC), the researchers have filed a patent to commercialize this sustainable cement process.
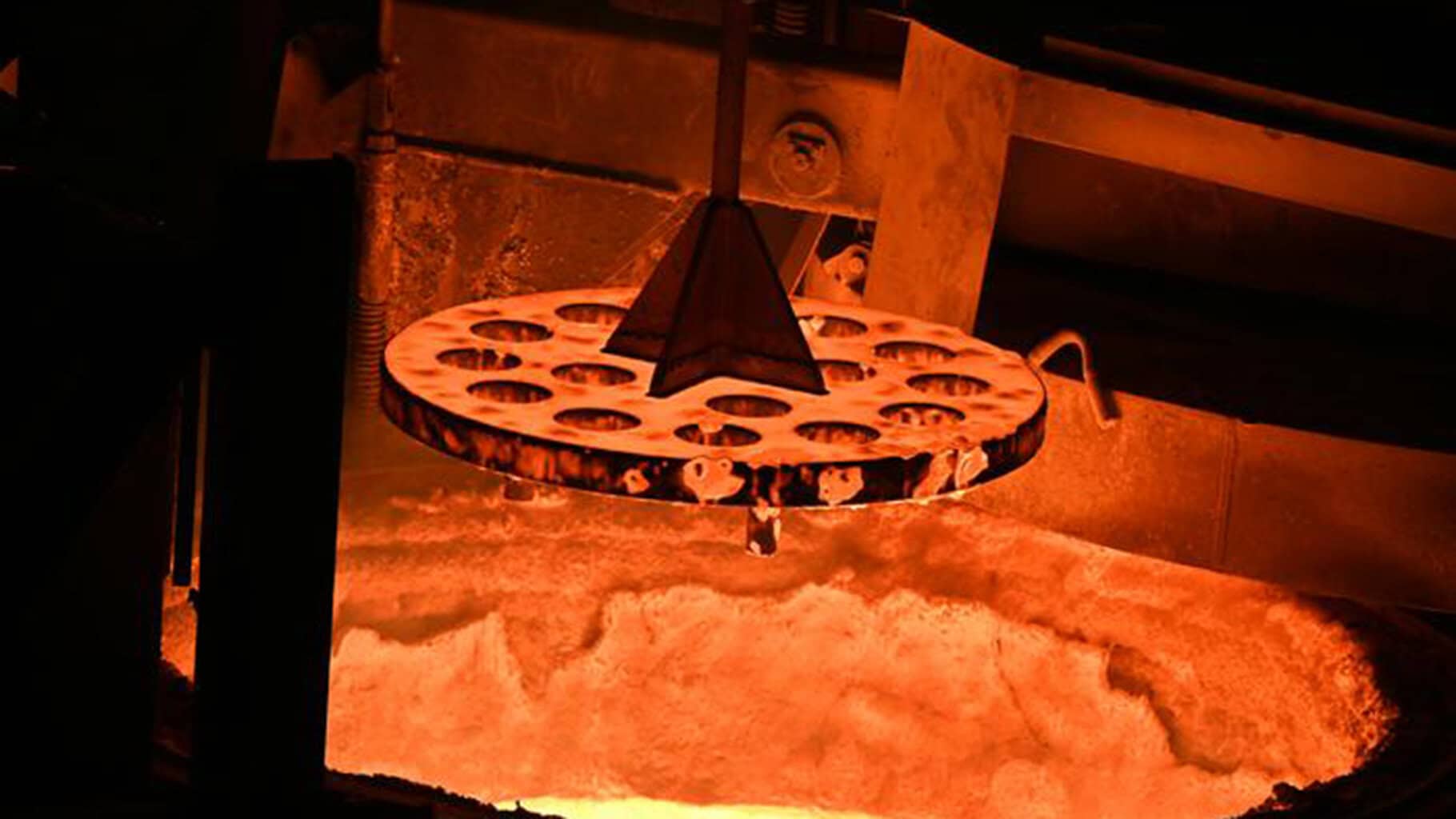
University of Cambridge Develops EAF-Based Technique for Zero-Emission Concrete Production and Cement Recycling
A team from the University of Cambridge has developed a ground-breaking technique for producing clean concrete on a large scale, potentially revolutionizing efforts to achieve net-zero emissions.
This novel approach to low- emission concrete leverages electric arc furnaces ( EAFs ), commonly used for steel recycling, to also recycle cement—the most carbon- intensive component of concrete.
This innovative process replaces salt flux, a material usually used in steel recycling to remove impurities, with cement, which has been hailed as” an absolute miracle” by experts.
Normally, salt flux becomes a waste byproduct known as slag. The end result is a recycled material suitable for new green material production by replacing it with recycled cement.
Concrete’s carbon footprint
Concrete, composed of sand, gravel, water, and cement, derives the majority of its emissions from the cement despite it being a small component by volume.
Cement production involves clinkering, a procedure that causes major CO2 to be released as limestone and other organic materials are heated to a temperature of about 1, 450°C.
Concrete ranks as the second most- used material internationally, just behind water, and accounts for almost 7.5 % of individual- caused CO₂ emissions.
The struggle to reduce concrete emissions while maintaining world supply is a significant impediment to decarbonization.
Although alternatives like fly ash can replace roughly half the cement in concrete, global supplies are insufficient to meet the estimated four billion tonnes of demand each year.
Modern efficient concrete production
No extra costs are associated with the new recycling method for producing steel or concrete.
Additionally, it significantly reduces the need for lime flux because it significantly reduces emissions from both industries.
The Materials Processing Institute’s most recent trials demonstrated that recovered cement could be produced effectively in an EAF, marking the first large-scale production of this kind.
This technique could ultimately produce zero-emission cement if it were powered by renewable energy.
The Materials Processing Institute’s EAF experimented with a variety of slags and salt mixtures to discover that cement clinker and iron oxide produce effective steelmaking slag, which is quickly cooled and causes reactivated cement.
Coming prospects and commercialisation
One billion tonnes of cement will be produced annually by 2050, which is roughly a quarter of the latest cement production, thanks to the rapid expansion of the Cambridge Electric Cement project.
The researchers, supported by Innovate UK and the Engineering and Physical Sciences Research Council ( EPSRC ), a division of UK Research and Innovation ( UKRI), have filed a patent to facilitate the commercialization of this sustainable cement process.